Flexible packaging films are widely needed by the global market. As a technology-based enterprise specializing in the production and operation of plastic packaging machinery, PLASTAR mainly produces multi-layer co-extrusion internal cooling upper traction rotary blown film extrusion machines, stretch film machines that are used in food, logistics, medicine, construction, household, agriculture, pharmacy, transportation, sanitation, electronics, automation engineering, and chemical industries.

High Berrier Film
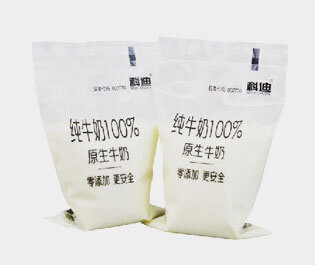
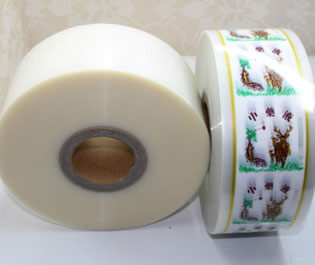
Food Composite Film
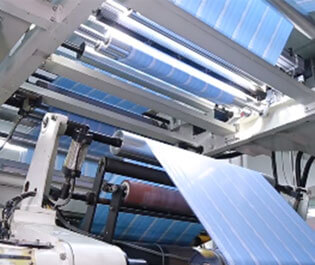
Agricultural Seed Packaging Film
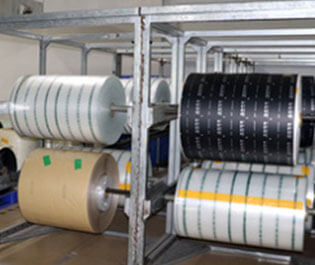
Vacuum Nylon Packaging Film
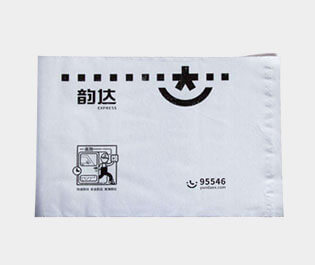
Courier Bag
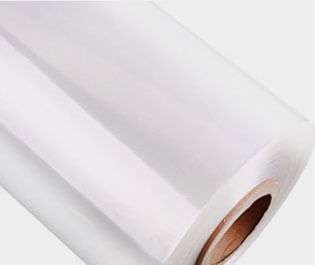
Shrink Film
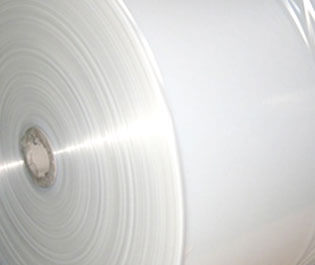
Stretch Sleeve Film
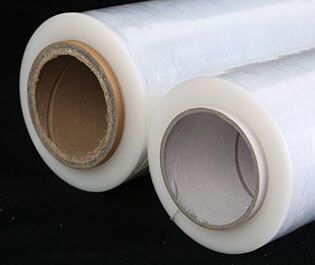
Self-adhesive Stretch Film
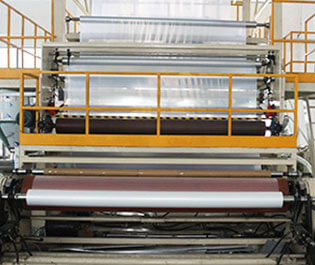
PE Anti-rust film
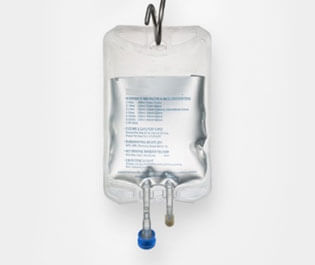
Drip Bag
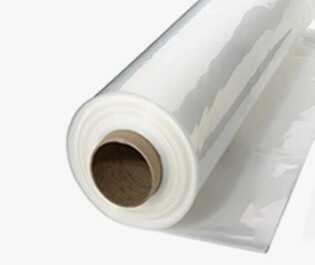
Modern Plastic Film
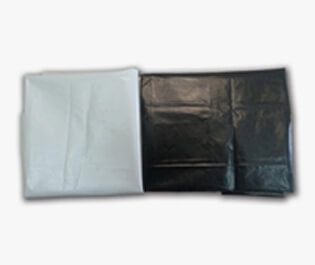
Mulch Film
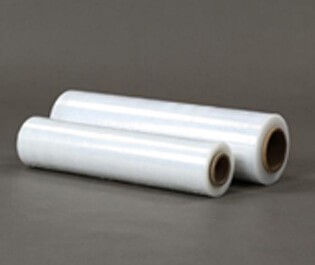
Forage Film Silage
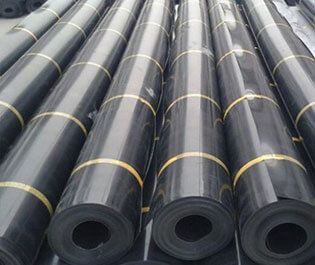
Impermeable Film
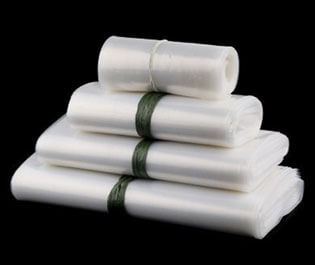
Fruit Bag
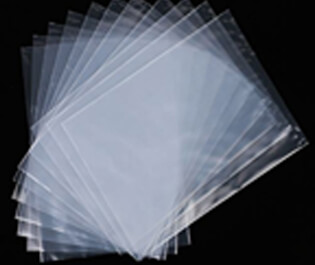
Medical Polyethylene Bag
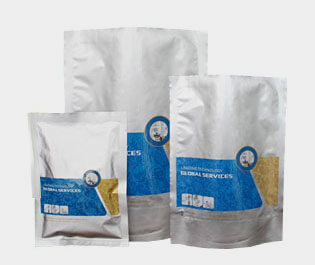
Aluminum Foil Composite Film
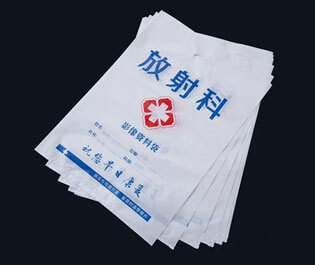
Medical Imaging Bag
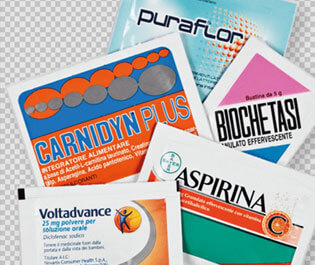
Drug Packaging Composite Film

Express Envelope Bags
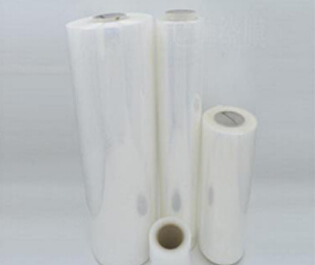
Heat Shrink Film
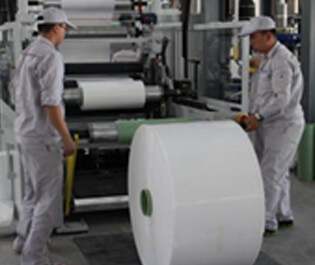
FFS Multi-layer Co-extrusion Heavy Packaging Bags
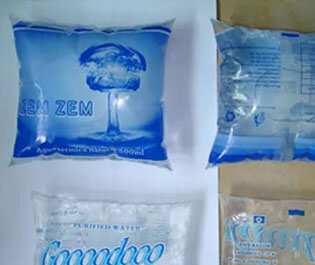
Water Bags
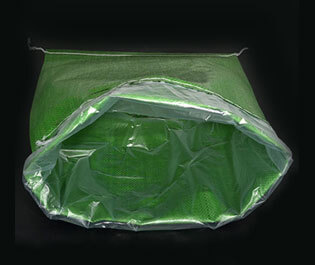
Woven Bags、Lining Bag of Boxes
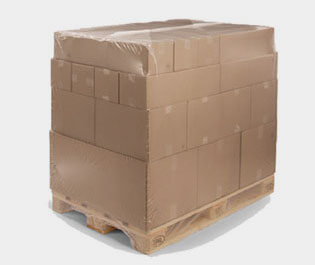
Pallet Shrink Bags
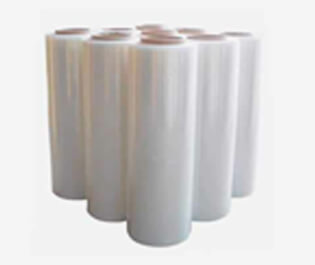
PE Shrink Film
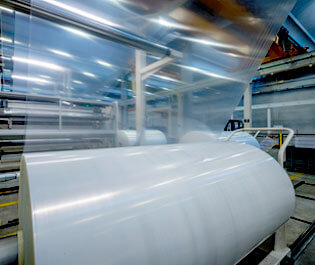
Outer Packaging Bags of Injection
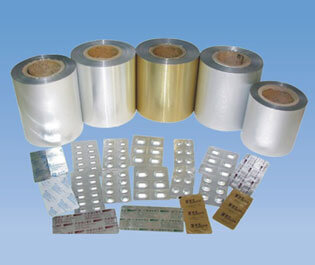
Medical Packaging Bags
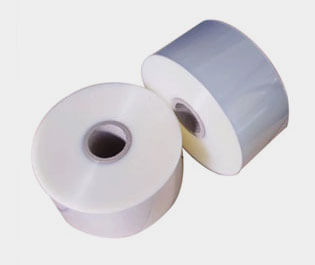
Disposable PE Examination Gloves
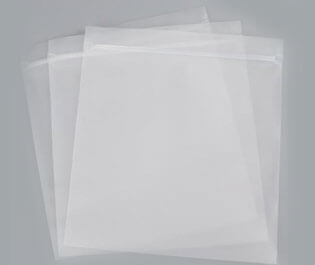
Medical Mask Packaging Bags
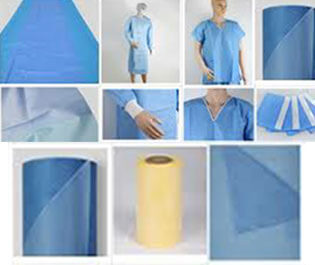
PE Breathable Film
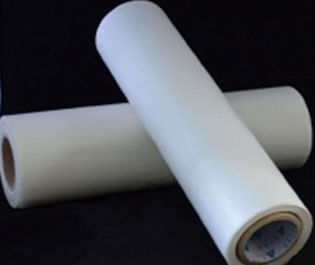
Self-adhesive Film
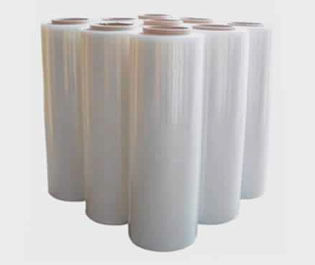
PE Shrink Film
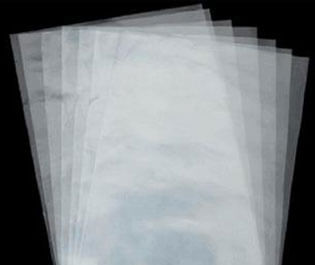
PE Protective Film
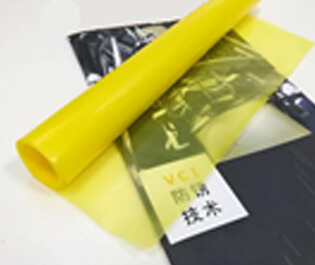
Anti-rust Film
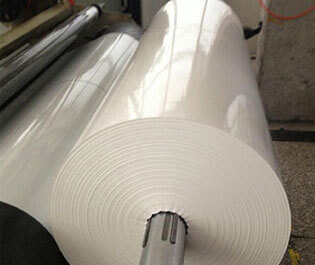
PE Tear Film
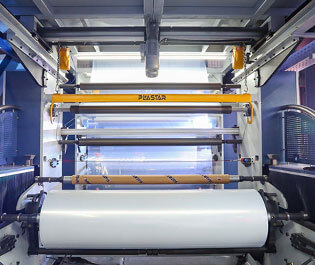
PE/PA Co-extrusion Film
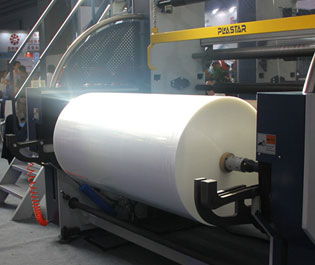
Square Bag
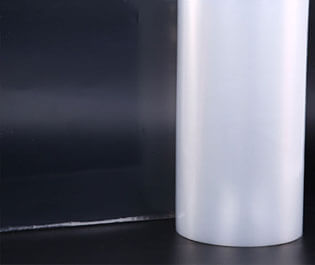
PE Heat Shrink Film
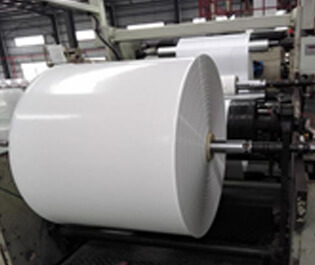
FFS Heavy Packaging
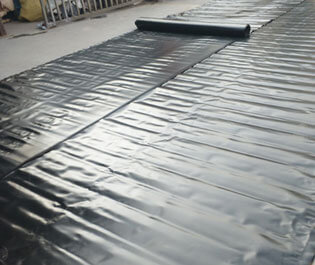
Geomembrane Film
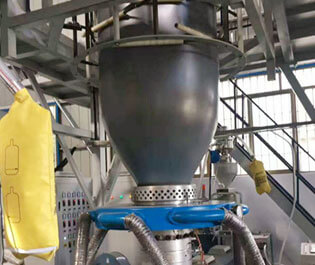
Ground Film
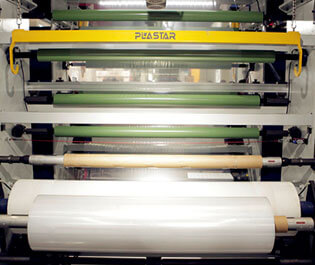
PE Anti-static Film
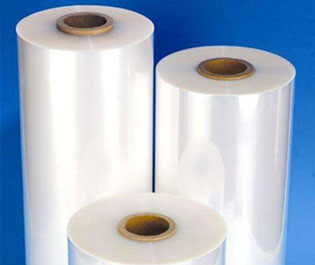
Carpet Protective Film
Global Certifications That Validate Our Blown Film Machinery
- Q1. What is recycled material, and what is the difference between the grades and prices of recycled materials?
- Q2. Prospects of the food packaging film industry.
- Q3. Why do we need a multi-layer co-extrusion blown film machine?
- Q4. What is the recommended blown film extrusion lines for the production of agricultural seed packaging film?
- Q5. What is the blown film extrusion line to use for vacuum nylon packaging film?
- Q6. What blown film extrusion machine is used for permeable films?
- Q7. What blown film extrusion line is used for PE/PA co-extrusion film?
- Q8. Why is extrusion molding used?
- Q9. What can blown film extrusion lines produce?
- Q10. Why are blown film extrusion lines used in food packaging industries?
- Q11. What blown film extrusion line is recommended for PE shrink film?
- Q12. What material is used for express envelop bags?
- Q13. Which material is not suitable for extrusion process?
- Q14. What is the recommended blown film extrusion lines for milk bags?
- Q15. What is the recommended blown film extrusion line for fruit bag?
- Q16. What materials are recommended for blown film extrusion machine?
- Q17. What materials can be used for blown film extrusion lines?
- Q18. What is the recommended blown film extrusion lines for high-barrier films?
- Q19. What blown film extrusion line is recommended for a medical packaging firm?
-
A1.
The recycled material refers to the plastic particles reshaped from recycled plastic film after being treated and then melted by a pelletizer.
The first-grade recycled material refers to the leftover material that is not contaminated with impurities, such as the edge of the online slitting of the blown film machine, and the plastic punched in the production of vest bags.
The recycled plastic particles processed with these leftover materials have better transparency. The quality of the particles formed by the pelletizer can rival that of the new material, so it is called the first-grade recycled plastic particles or the super-grade recycled plastic particles.
The second-grade recycled material refers to the recycled film that has been used once. It is judged by observing the transparency, brightness and surface roughness of recycled plastic particles formed by the pelletizer.
The third-grade recycled material refers to materials that have been used twice or more. The elasticity, toughness and other properties of the recycled plastic particles formed by the pelletizer are not outstanding, so the material can only be used for injection molding. The first-grade and second-grade recycled plastic particles can be used for film blowing.
Price grades of recycled materials:
- First-grade recycled plastic particles: 70-80% of the price of new raw materials;
- Second-grade recycled plastic particles: 50-70% of the price of new raw materials;
- Third-grade recycled plastic particles: 30-50% of the price of new raw materials;
- The above price ratio is for reference only
-
A2.
About 30% of food worldwide is wasted due to the lack of proper packaging. By 2050, the global population is expected to reach 10 billion. As urbanization is accelerated, proper food packaging is urgently needed during transportation from the place of origin to various cities to avoid unnecessary loss.
In addition, as the industry is growing, a great deal of food packaging applies barrier films from Blown Film Extrusion Lines to extend the shelf life, which reduces costs and increases sales and storage cycles.
Therefore, cutting-edge barrier films composed of 7 to 9 layers are in great demand in the food industry.
-
A3.
Compared with the single-layer blown film machine, the multi-layer co-extrusion blown film machine requires more screws and purchase costs to produce the film.
The selection of the multi-layer co-extrusion blown film machine depends on the application scenarios of the target film produced. If the film produced is mainly used as the packaging material for heavy packaging, high-end food bags, vacuum packaging bags, liquid packaging bags, etc., it needs functions including fragrance preservation, freshness preservation, corrosion protection, air tightness, and extended shelf life. A single-layer and single-characteristic film can never live up to these functions.
To produce a film that is qualified as a packaging material, and blow and co-extrude materials with a variety of characteristics(such as breathability, heat preservation, toughness, etc.) to form a multifunctional plastic composite film, we have to choose a multi-layer co-extrusion blown film machine.
The purpose we choose a multi-layer co-extrusion blown film machine is to give full play to the advantages of multiple materials and avoid the shortcomings of a single material or single-layer blown film machine. Taking the PP/PE co-extrusion blown film machine as an example, the machine combines the high hardness of the PP material and the high brightness of the PE material to produce a film that has the characteristics of both.
We have the following models of multi-layer co-extrusion blown film machines:
- Two-layer co-extrusion blown film machine,
- Three-layer co-extrusion blown film machine,
- Five-layer co-extrusion blown film machine,
- Seven-layer co-extrusion blown film machine, etc.
For example, The five-layer co-extrusion blown film machine mainly uses plastic particles with gas barrier properties, such as HDPE, MHDPE, LDPE, LLDPE, MLLDPE, PA, EVOH, etc., to produce food packaging films that require fragrance preservation, freshness preservation, corrosion protection, air tightness, and extended shelf life.
Multi-layer co-extrusion is to extrude multiple layers of plastic particles from one die at the same time. Most food packaging films and special films are produced by this co-extrusion lamination.
-
A4.
ABA three-layer blown film extrusion line and ABC three-layer blown film extrusion line are recommended for the production of agricultural seed packaging films.
The ABA three-layer blown film extrusion lines are effective for flexible production applications such as agricultural seed packaging films as they boost production and lower the cost of production.
The ABA three-layer blown film extrusion lines have two main motors that provide three-layer extrusion, the main machine gives the inner and the outer coating layers while the other machine is in charge of the inner filling layer; the goal of this to help you reduce cost and consumption while producing agricultural seed packaging films.
ABC three-layer blown film extrusion lines are designed to be used for the production of a wide range of packaging films such as agricultural seed packaging film, liquid packaging film, electrostatic protection film, and many others.
Both ABA three-layer blown film extrusion lines and ABC three-layer blown film lines have a high degree of hardness and resistance to wear, which makes them suitable for the production of agricultural seed packaging films.
-
A5.
The recommended blown film extrusion line used for the vacuum nylon packaging film is a five-layer blown film extrusion line.
PLASTAR's five-layer blown film line has been particularly designed to produce a wide range of applications such as oil packaging, milk bags, vacuum packaging of solid containers, and many more.
Five-layer blown film extrusion line, just like every other type of PLASTAR's blown film extrusion line, is equipped with dual-alloy forced-feeding screws that feature excellent hardness and wear resistance.
This makes the PLASTER five-layer blown film efficient in the production of vacuum packaging of solid containers as they have a high level of hardness and wear resistance.
Five-layer blown film extrusion lines also use an advanced five-layer plane stacking mold, which makes optimizes the layout due to thermofluidics, which helps watch the fluid condition through the 3D simulation software.
Five-layer blown film extrusion lines also help reduces the amount of time your blown film extrusion line is unavailable due to maintenance because it ensures the reduction of waste during the particle replacement procedure while printing vacuum Nylon packaging film.
-
A6.
ABA Three-layer blown film extrusion lines and ABC three-layer blown film extrusion lines, and ABA three-layer blown film extrusion lines are recommended for the production of permeable films.
ABA Three-layer blown film extrusion lines and ABC three-layer blown film extrusion lines help reduce production cost while producing materials and also has high wear resistance, thereby making them durable enough for the production of permeable films.
Both ABA three-layer blown film extrusion lines and ABC three-layer blown film extrusion lines are equipped with upgraded features such as centralized feeding, batching, and weight control, which are all blended into the touch screen to help enhance an easier and faster production of permeable films.
-
A7.
The blown film extrusion line that is used for PE/PA co-extrusion film is the five-layer co-extrusion blown film line.
This blown film extrusion line can be used to produce a variety of film packaging across different industries.
This blown film extrusion line has an excellent hardness feature, and it is highly wear-resistant.
It can produce a lot of films consequently without fail at a very high speed and high pressure.
The forced-feeding screw of this blown film extrusion line has a service life that is 3 to 5 times higher than an ordinary screw.
It has an advanced plane stacking mold that produces a high degree of polishing and coating of your materials, and it has the capability of cleaning itself after producing your material, with reduced wastage of material.
This lessens the downtime it has when a particle in it is being replaced or when the blown film extrusion line is being maintained.
Whether you want to produce PE/PA co-extrusion film or another packaging film, the five-layer co-extrusion blown film line will do the work while you don't have to worry about whether you will get a quality product because you will.
-
A8.
Extrusion molding is used due to its volume of productivity, speed, low cost, flexibility, and post-extrusion altercation option.
With extrusion molding, you can produce a large volume of plastics effectively and efficiently.
It is also cheaper than other molding types in that you can reuse waste materials, making production less expensive, unlike with other molding types like blow molding.
Your blown film extrusion machine can also work for long hours, allowing for long productivity time for as long as 24 hours in a day, increasing the productivity of your machine and products.
Extrusion molding is also flexible in that it is flexible in the production of materials, and can produce products with cross-section and products with mixed plastic attribute.
With extrusion molding, you can also alter production because after products are extruded, they remain warm, giving room for you to mold and remold them into more desirable shapes.
Your machine can produce up to 60 feet length products at a go. You tend to be more productive with extrusion molding, and at a cheaper cost compared to other molding types.
- A9. Blown film extrusion lines are used to produce polymer films used by packaging industries, which include shrinking wrap films, stretch films, packing films, shopping bags, laminating films, and many other packaging materials.
-
A10.
If you do thorough research, you will discover that about thirty percent of food across the globe gets to become waste as a result of lack of proper packaging.
Scientists have concluded that the population of the world is likely to reach several ten billion and when this is obtained, and even before then, provision should have been made for proper packaging of foods during the period of transporting them from one part of the world to the other to avoid loss.
Furthermore, as the industry grows, the packaging of food has been on the increase, and a great deal is applied to extend its longevity.
That is why blown film extrusion lines have been chosen over every other machine across the world to be used for the flexible packaging of food.
Blown film extrusion lines are generally accepted and chosen over other products by the global market because it is a technology-based enterprise that specializes in the operation and production of plastic packaging machinery.
Their main products are stretch film machines, multilayer co-extrusion internal cooling upper traction rotary blown film extrusion lines, and they are used in various industries such as electronics, logistics, chemical industries, construction, transportation, and food inclusive.
-
A11.
The PE shrink film can be produced with more than one blown film extrusion line, and you can try either of them.
The two blown film extrusion lines that you can use to produce PE shrink film are the ABA three-layer co-extrusion blown film line and the ABC three-layer co-extrusion blown film line.
The ABA three-layer co-extrusion blown film line is very flexible and can save your organization some production costs and conserve energy.
You can recycle materials for repeated production with this blown film extrusion line and save costs.
It also has a wear resistance, which gives you a competitive advantage, and at the same time, it helps you reduce cost, consumption, and energy and save the number of main machines.
The ABC three-layer co-extrusion blown film line is a general-purpose blown film line, and it can be used to produce different packaging films, including PE shrink film and other heavy packaging film.
Either of the blown film extrusion lines works for the purpose you want to use it for, and it will produce the PE shrink film you have in mind effortlessly.
Whichever one you go for, you can rest assured that you will get your desired result without defects.
-
A12.
The materials used for express envelop bags are the materials you can use with the ABA three-layer blown film extrusion lines and the ABC three-layer blown film extrusion line.
The material used in these blown film extrusion lines is HDPE, LDPE virgin raw material, recycled material, CaCO3 compound, biodegradable material, master starch, additive, mLLDPE, PP, EVA, LLDPE, etc.
If you want to produce quality express envelop bags, you have a range of material options to choose from.
-
A13.
The extrusion process is not suitable for iron and iron metal extrusion.
Producing an object with iron alloys may ruin your blown film extrusion machine because they are not fit for production.
Some of the plastic materials fit for the extrusion process are polyethylene, polypropylene, nylon, polycarbonate, acrylic, polyvinyl chloride, ABS, polystyrene, and nylon.
Any other material apart from the iron will extrude perfectly shaped objects that you have in mind.
The materials that are commonly used for extrusion are metals, polymers, ceramics, concrete, and foodstuff.
However, before you pick out the materials to use in your machine, consider the viscosity and the melting point differences of the materials.
The viscosity of material has to do with its resistance to flow. You know your material needs to flow so that it can be easily extruded out of the die.
-
A14.
The recommended blown film extrusion line for Milk bags is specifically of two types: AB two-layer blown film extrusion line and ABA three-layer blown film extrusion line.
The production line AB two-layer blown film extrusion line is suitable for blowing high-density polyethylene, low-density polyethylene, and linear low-density polyethylene, which are generally used in the production of courier bag film and two-color film.
ABA three-layer blown film extrusion line gives room for more flexible production than producing milk bags requires.
ABA three-layer blown film extrusion line also helps save energy consumption and cost, which makes producing milk bags cheaper for you.
The production line of both AB two-layer blown film extrusion lines and ABA three-layer blown film extrusion lines are equipped with advanced automation features such as centralized feeding, weight control, and batching.
All of these unique functions have been integrated into their touch screen to enhance productivity and ease during the production of milk bags.
-
A15.
The blown film extrusion extrusion line suitable for producing fruit bags is PLASTAR's single-layer blown film extrusion line.
The single-layer blown film extrusion line produced by PLASTER is most suitable for the production of fruit bags.
The single-layer blown film extrusion line helps you maximize the utilization of heat energy while producing fruit bags by putting an end to the use of cooling fans, thereby increasing your production output while reducing your energy consumption rate.
PLASTAR's single-layer blown film extrusion line makes use of a single-layer cone mold that helps reduce downtime maintenance and reduce particle waste in the particle replacement procedure in the production of fruit bags.
This happens because the single-layer cone mold ensures that each runner can clean itself under the PLASTAR's high-speed screws' intense pressure and high-speed scouring after the intense degree of polishing and coating.
-
A16.
Blown film extrusion can use plastic materials only.
The different types of plastic materials that can be used include:- PVC: PVC comes in different colors and levels of flexibility and rigidity and is highly durable.
- ABS: ABS is strong, and are commonly used to produce household materials.
- Thermoplastic elastomers: Thermoplastic elastomers are widely used due to their stability.
- Polyurethane: Polyurethane is commonly used in oil and gas industries due to its high abrasion resistance.
- Polypropylene: Polypropylene is strong and resistant to organic solvents.
-
A17.
Polyethylenes, which include LDPE, LLDPE, and HDPE polymers, are the most common materials used in blown film extrusion lines.
You need to understand the material properties of the resin you want to use for your blown film extrusion line.
As much as you would want to use as many materials as you want so as the maximize your blown film extrusion line utilization, it is also important to note that blown film extrusion lines are different and are not designed the same.
Therefore, blown film extrusion lines will not be able to accommodate all the types of materials available, which is why polypropylene and polyethylene (LDPE, HDPE, and LLDPE) are mostly used because they work effectively and with minimum complications with a majority of blown film extrusion lines.
-
A18.
The recommended blown film extrusion lines for high-barrier films are PLASTAR's 5-layer blown film extrusion lines.
PLASTAR's 5-layer blown film extrusion lines have been designed specifically to be used to produce symmetric barrier films and asymmetric barrier films.
PLASTAR's five-layer blown film extrusion line makes use of the most upgraded five-layer plane stacking mold, which helps optimize the layout due to the thermofluidics present and also monitors the fluid condition with the assistance of five-layer blown film extrusion line simulation software, which makes it efficient in the production of High Barrier films.
You do not have to worry about waste getting stored up in the waste and particle replacement place in the production of your high barrier films because the PLASTAR five-layer blown film extrusion line help reduce waste during production as each runner can clean itself under intense pressure and high-speed scouring of PLASTAR's high-speed screws.
Additionally, PLASTAR's 7/9 Layer Blown Film Extrusion Lines are also an excellent choice for producing high-barrier films. These lines offer lots of advanatges for this application.
-
A19.
The recommended blown film extrusion line for medical packaging firm is the five-layer co-extrusion blown film line.
The five-layer co-extrusion blown film extrusion line can be used to produce different products across different fields, and the medical field isn't left out.
It can be used to produce symmetric barrier film and asymmetric barrier film.
Therefore, if you want to produce any different medical packaging firm, your go-to blown film extrusion line is the five-layer co-extrusion blown film extrusion line.
You can make different packaging firms like medical mask packaging bags, outer packaging injection bags, medical mask packaging bags, disposable PE examination gloves, medical packaging bags, drip bags, and other packaging bags for different medical packages.
Although there are other blown film extrusion lines that can produce some of these medical packages, the five-layer co-extrusion blown film line can produce any medical packaging you want.
All you have to do is select the raw materials and produce any medical packaging accessories you want.
The five-layer co-extrusion blown film extrusion line is a good blown film extrusion line to use in producing all your medical packaging firms.
It is equipped with the necessary features needed to produce a variety of medical packaging firms.