Advanced Barrier Film Production Equipment
Five-layer Co-extrusion Blow Film Machine
Our 5-layer co-extrusion blown film machines, known as our Blown Film Extrusion Lines for Barrier Film, can satisfy most film production applications in the industry. These versatile machines produce both symmetric and asymmetric barrier films suitable for food packaging, oil packaging, milk bags, vacuum packaging of solid containers, and other applications.
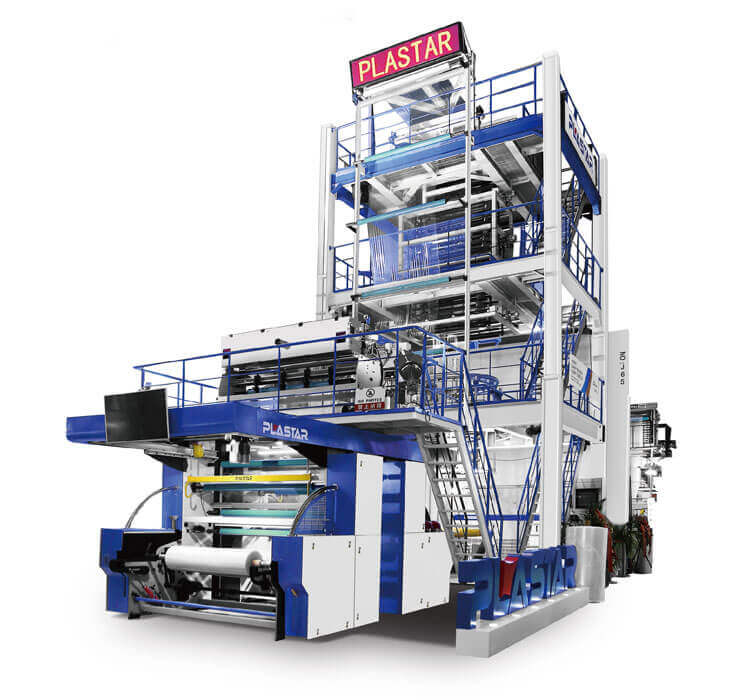
Forced feeding main machine
All main machines of PLASTAR adopt dual-alloy forced-feeding screws that feature excellent hardness and wear resistance. It can still plasticize a large number of particles under the environment of high speed and high pressure. The service life can reach 3-5 times of ordinary screws.
Plane stacking mold
The five-layer co-extrusion blown film machine production line uses the most advanced five-layer plane stacking mold. We optimize the layout by virtue of thermofluidics and observe the fluid condition with the help of 3D simulation software. We are sure that after a high degree of polishing and coating, each runner has the ability to clean itself under the high pressure and high speed scouring of PLASTAR’s high-speed screws. It will reduce waste in the particle replacement process and shorten the downtime of maintenance.
Advanced automation module
The production line of five-layer co-extrusion blown film machines has advanced automation functions, such as centralized feeding, batching, weight control, IBC internal cooling, automatic thickness control, and automatic central winding. All functions are integrated on the touch screen, thus simplifying operations and increasing productivity.
Model | SJ-5L1500 |
---|---|
Suitable Material | HDPE, LDPE, LLDPE, EVA, Nylon etc. |
Film Width | 1500 mm |
Film Thickness | 0.03 - 0.2 mm |
Max. Output | 300kg / h |
Extruder | |
Screw Diameter | 55mm * 4 / 60mm * 1 |
Screw L/D | 30:1 |
Barrel Cooling | Water Cooling |
Main Motor Power | 30kw * 4; 37kw * 1 |
Total Power | 200kw |
Die Head | |
Die Head Type | Five layers with inner cooling device |
Air Ring | Double lips air ring |
Traction Roller Width | 1700 mm |
Effective Width | 1500 mm |
Traction Speed | 45m / min |
Winding Unit | |
Wingding Type | Friction type automatic single / double winder |
Wingding Speed | 5 - 45m / min |
Voltage | 380V, 50Hz |
Dimension | About 10 * 6.0 * 12.5 m |
Weight | About 16 T |
Video
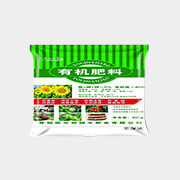
Vacuum Packaging of Solid Containers
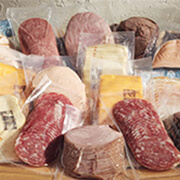
Food Vacuum Packaging
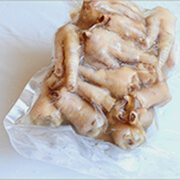
Food Vacuum Packaging
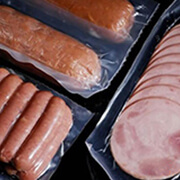
Food Vacuum Packaging
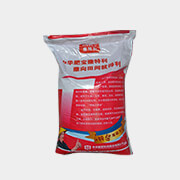
Food Vacuum Packaging
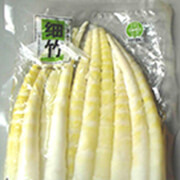
Food Vacuum Packaging
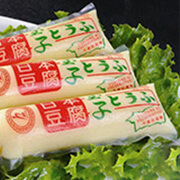
Oil Packaging
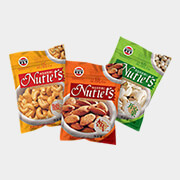
Vacuum Packaging of Solid Containers
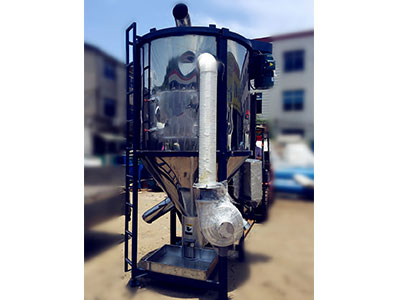
Mixing Machine
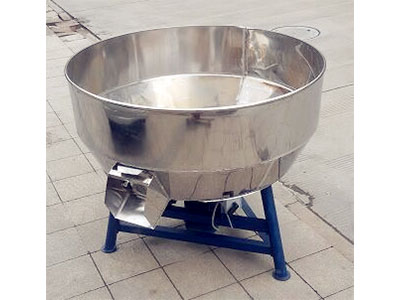
200 kg Mixing Machine
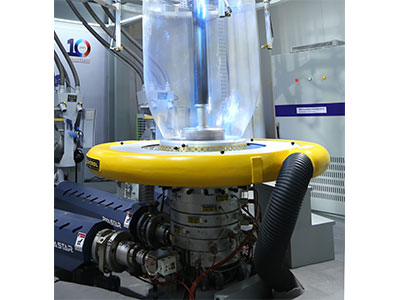
Automatic Air Ring
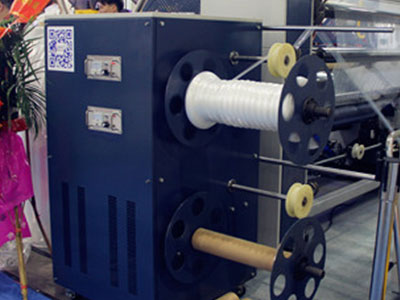
Leftover Material Recovery Machine
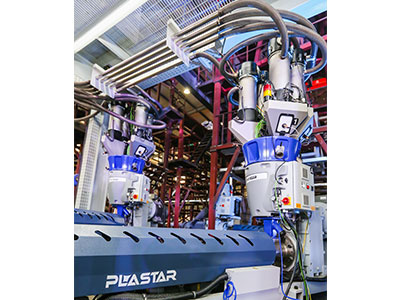
Four-component Feeder
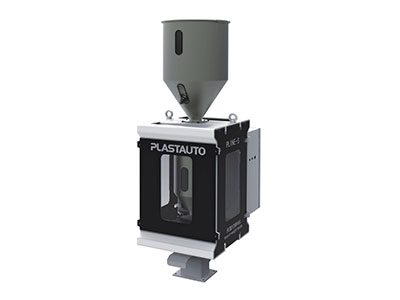
Loss-in-weight Feeder
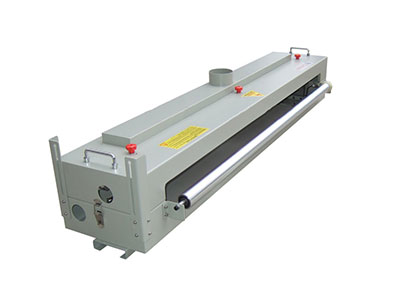
Corona Treatment Rack
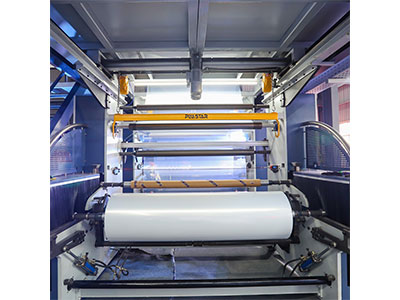
Manipulator
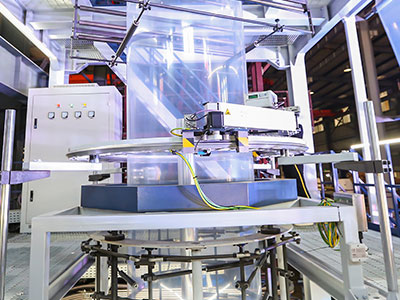
Automatic Thickness Measurement Device
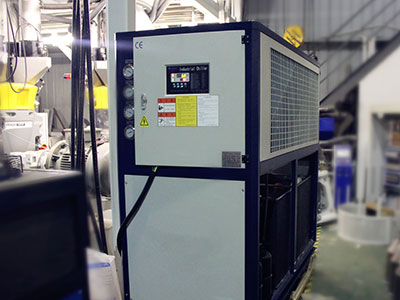
Cold Water B
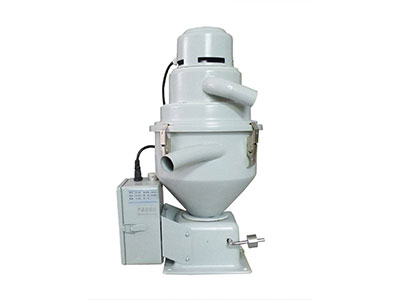
Suction Machine
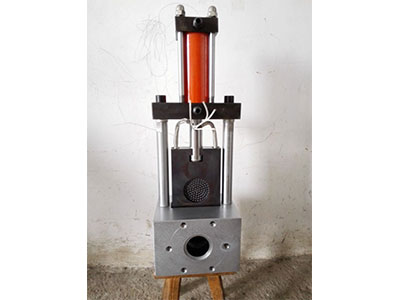
Hydraulic Screen Exchanger
Global Certifications That Validate Our Blown Film Machinery
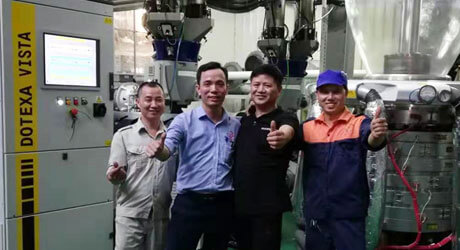
Vietnam - Five-layer Co-extrusion Blown Film Machine
In October 2019, a Vietnamese customer successfully installed the 1600 mm ABCDE five-layer co-extrusion blown film machine.
- Q1. Where is the blown film machine factory?
- Q2. What certificates do your blown film machines have?
- Q3. What is the general delivery time of blown film machines?
- Q4. Can I visit the blown film machine production plant and watch the commissioning process?
- Q5. What is the payment method for blown film machine orders?
- Q6. What is the next step after blown film machines arrive at the destination factory?
- Q7. What kind of after-sales service do you provide if the blown film machines encounter technical problems or part damage?
- Q8. Does your blown film machine have an operation manual and an electrical schematic diagram?
- Q9. What are the main markets of your blown film machines?
- Q10. How long is the warranty period of blown film machines?
- Q11. Where is blown film extrusion machine manufacturer located?
- Q12. Who are blown film extrusion line manufacturers?
- Q13. Where are blown film extrusion line manufacturers?
- Q14. Why are PLASTAR blown film machine trusted?
- Q15. Why blown film extrusion line manufacturers?
- Q16. What is the warranty period of blown film extrusion lines?
- Q17. What is the delivery period of blown film extrusion machines?
- Q18. What blown film extrusion machines are for sale?
- Q19. Are all blown film lines customizable?
- Q20. What is the blown film extrusion machine price?
- Q21. What is the payment method for blown film extrusion lines?
- Q22. What happens after blown film extrusion line is delivered?
- Q23. What are multi-layer blown film extrusion lines?
- Q24. Are there used blown film extrusion machine for sale?
- Q25. What is recycled material, and what is the difference between the grades and prices of recycled materials?
- Q26. Prospects of the food packaging film industry.
- Q27. Why do we need a multi-layer co-extrusion blown film machine?
- Q28. What is the recommended blown film extrusion lines for the production of agricultural seed packaging film?
- Q29. What is the blown film extrusion line to use for vacuum nylon packaging film?
- Q30. What blown film extrusion machine is used for permeable films?
- Q31. What blown film extrusion line is used for PE/PA co-extrusion film?
- Q32. Why is extrusion molding used?
- Q33. What can blown film extrusion lines produce?
- Q34. Why are blown film extrusion lines used in food packaging industries?
- Q35. What blown film extrusion line is recommended for PE shrink film?
- Q36. What material is used for express envelop bags?
- Q37. Which material is not suitable for extrusion process?
- Q38. What is the recommended blown film extrusion lines for milk bags?
- Q39. What is the recommended blown film extrusion line for fruit bag?
- Q40. What materials are recommended for blown film extrusion machine?
- Q41. What materials can be used for blown film extrusion lines?
- Q42. What is the recommended blown film extrusion lines for high-barrier films?
- Q43. What blown film extrusion line is recommended for a medical packaging firm?
- Q44. What is 5-layer blown film extrusion machine?
- Q45. What is the difference between ABA three-layer blown film co-extrusion machine and ABC three-layer co-extrusion blown film machine?
- Q46. What is 3-layer co-extrusion machine?
- Q47. What are three-layer blown film extrusion lines?
- Q48. What are the benefits of 7/9/11 blown film lines over 3 or 5 layers?
- Q49. What is stretch hood three layers blown film extrusion line?
- Q50. What are 3-layer co-extrusion plastic blown film lines?
- Q51. What is mono-layer blown film extrusion machine?
- A1. Our factory is located in Zhenzhong East Road 85#, Juyu Town, Wencheng County, Wenzhou City Zhejiang Province, China. You can take a plane to Wenzhou Longwan Airport or take a train to Rui’an Station. Please make an appointment with our sales specialist in advance, and our driver will pick you up at the station when you arrive.
-
A2.
Our factory fully implements the ISO9001:2015 quality management system and has passed the TUV certification, which covers design, production, and delivery. Our purpose is to ensure the quality and safety of blown film machines from the source.
If you are a global customer who wants to buy a blown film machine, the safety requirements of different countries will take you aback. We have the most widely recognized Swiss SGS certification and EU safety CE certification, which can meet the safety requirements of most countries in the world, thus removing every obstacle for you to place orders.
- A3. The production of a blown film machine usually takes about 30 to 60 working days, depending on the size and configuration of the machine. Our factory implements customized production of blown film machines, and an accurate delivery date will be agreed upon during the negotiation process.
- A4. Of course, you can. We are a professional blown film machine manufacturer in China, and we welcome you to visit us at any time. We will pick you up at Wenzhou Longwan Airport or Rui’an Railway Station. If you want to see the blown film machine you are interested in during your stay, you can also make an appointment with our sales specialist. We will show you the operation of the blown film machine to make your journey more fruitful.
- A5. We will start production when we receive a 30% deposit of the full order price. After we complete the production within the delivery period and receive the 70% final payment, we will send you the images and videos of the blown film machines being packaged and shipped.
- A6. When our blown film machines arrive at your factory, our engineers will arrive at your factory before the appointed time. They will assemble and debug the blown film machines according to the factory environment. When the machines can operate normally, they will start to train your staff on the operation, production, and routine maintenance of the blown film machines according to the equipment properties, so as to make sure that your employees are competent enough to operate the blown film machines.
-
A7.
We will remotely communicate with you via video to tell you how to solve the technical problems of blown film machines. If the problem cannot be solved, we will consider sending an engineer to your site.
If the damaged part (non-consumable part) is within the warranty period, we will provide you with another one free of charge, with the transportation charges paid by our factory.
- A8. Yes, although most of our blown film machines are customized, they are all independently designed before being put into production. Each blown film machine is accompanied by an operation manual and electrical schematic diagram, both in Chinese and English.
- A9. As of December 2019, our blown film machines had been sold to 93 countries around the world, mainly including China, Europe, the Middle East, Southeast Asian countries, the United States, Canada, and Latin American countries. Boasting a wealth of logistics and freight experience, we can give you full support or advice on freight duties and logistics costs while ensuring the safe arrival of blown film machines.
- A10. All our blown film machines have a one-year warranty, starting from the date when the blown film machine arrives at your factory and completes commissioning. During this period, we will provide a fully free warranty for the whole machine, except for consumables.
-
A11.
PLASTAR is a professional blown film extrusion machine manufacturer that produces and delivers complete blown film extrusion machines to manufacturers, distributors, and those in the packaging industry.
PLASTAR blown film extrusion machine company is located in Zhenzhong East Road 85#, Juyu Town, Wencheng County, Wenzhou City Zhejiang Province, China.
To visit PLASTAR, board a plane to Wenzhou Longwan Airport, or you can visit them via train by going to Rui’an Station.
Before your visit to PLASTAR, please book an appointment with their sales specialist beforehand.
When you book an appointment with PLASTAR, a blown film extrusion machine manufacturing specialist, the driver would come and pick you up at the station you are at.
-
A12.
Blown film extrusion line manufacturers are professionals in the blown film line company. They work tirelessly to ensure they deliver satisfactory machines to their customers.
The blown film extrusion line manufacturers deliver complete blown film extrusion line services ranging from design to development and production of the product.
They are committed to intelligently producing blown film extrusion lines thereby reducing the number of staff and manpower in your company; they help in inspecting the line of products and also improve the quality of products.
This set of highly skilled professionals is one of the few state-level high-tech enterprises recognized by the National Department of Science and Technology in the state of China and perfectly finishes up the tasks their customers deliver.
The production of the blown film extrusion line manufacturers has utmost reverence for the ISO9001:2005 quality system and has successfully undergone the certification of the TUV.
Blown film extrusion line manufacturers are keen on accepting trade globally, and they have also passed through the SGS certification of Switzerland and the CE certification of the EU. These two certifications are widely recognized by the most wide-ranging nations across the world.
The above features of the blown film extrusion line manufacturers qualify them to be keen on supporting the businesses of their customers all over the world.
-
A13.
Blown film extrusion line manufacturers have their offices situated in different locations across the universe within a short period of their arrival in the global market.
You can find them in about ninety-three countries in the cosmos, including the Middle East, the United States of America, Latin American Countries, China, Europe, Southeast Asian countries, and Canada, to mention but a few.
If you are keen on locating them, let's say, you do not want to order their products online but to see for yourself what they do in their company, you can easily locate them in these places which will be mentioned below.
They are situated at Zhenzhong East Road 85#, Juyu Town, Wencheng County, Wenzhou City Zhejiang Province, China.
If you consider booking an appointment with one of their top professionals who is a specialist in offering sales, ensure to take the next flight from your country of destination to Wenzhou Longwan Airport and it is also possible for you to take a train, depending on your convenience to Rui'an Station.
You need to have their sales specialist informed before your visit so that proper arrangements will be made for your pick up by their driver immediately after you arrive.
-
A14.
PLASTAR’S blown film extrusion machine is trusted by more than 3000+ customers for many reasons.
PLASTAR has been existing for more than 30 years and is trusted by all because they master the core of the technology flow in the process of blown film machine.
PLASTAR also uses more than ten German machining center production lines in the processing of the mold of their blown film extrusion machines.
Their blown film extrusion machines have also gotten different certifications worldwide.
Their machines have passed the CE certification of the EU, the SGS certification of Switzerland, and the German TUV certification.
These certifications back PLASTAR’S claim that their machines are safe, environmental-friendly, of good quality, meet safety qualifications all around the world, and match customers’ requirements and satisfaction.
Their blown film extrusion machines are produced in varieties and can be customized according to customers’ requests as well to suit their needs and their equipment.
Also, PLASTAR is committed to creating intelligence automation of its blown film machines to increase productivity of the machines.
The production of these intelligent automation lines of machines has helped relieve the dependence on skilled workers, reduce productivity defects, and enhance overall efficiency in producing the objects for their customers.
-
A15.
Blown film extrusion lines are manufacturers of world-class technology-based professional plastic packaging machinery.
Internal cooling devices, stretch film machines, and multilayer co-extrusion blown film extrusion lines, among many others, are the main products produced by manufacturers of blown film lines.
These products are sold to various countries such as India, Turkey, Yemen, Europe, Pakistan, the Middle East, and other countries across the globe.
Most of the products manufactured by blown film extrusion lines are specially modified and are all designed autonomously before they are finally produced.
It's okay to note that all blown film extrusion lines have electrical schematic diagrams and operation manuals written in both English Language and Chinese.
Blown film extrusion line has been widely recognized and patronized by a huge number of people living across ninety countries in the world.
They have more than thirty years of experience and an entirely complete set of technology in their possession.
Blown film extrusion line has been recognized as a company that meets the precautionary rules and regulations of most countries in the biosphere.
-
A16.
Blown film extrusion line, a technology-based professional plastic packaging machinery company, is a trusted company, and they are widely accepted all over the world because of the exceptional services they render.
As a result, blown film extrusion lines have a period of one-year warranty for any product you purchase from them apart from consumables.
This period of one year starts on the day the blown film extrusion line arrives at your company after you must have ordered it. Also, the 365 or 366-day assurance starts reading at the point when the engineers have finished commissioning the blown film extrusion line.
Blown film extrusion lines are customer-friendly such that for the period of the one year in which you have a service contract with their company, you are at liberty to use their machine and have them freely fix it in cases where it becomes faulty.
-
A17.
PLASTAR is in charge of Blown film extrusion machines in large and quality quantities to distributors, wholesalers, and those in the packaging industry across the globe.
At PLASTAR blown film extrusion machine manufacturing company, the production of blown film extrusion machines takes place between 30 to 60 working days.
However, the length of the period is greatly determined by the size and configuration of the machine because PLASTAR blown film manufacturers are committed to producing customized machines to create a personalized experience for end-users.
To do this, PLASTAR produces and designs blown film machines according to the size and configuration that best suits the needs of clients and end-users.
Once, the configuration and size are determined, PLASTAR would provide the exact date that a client’s blown film machine would be available.
-
A18.
There are many different types of blown film extrusion machines available for sale.
They include: -
A19.
All blown film lines produced by PLASTAR, a professionally blown film extrusion line manufacturer, are customizable.
PLASTAR is a top-rated blown film line manufacturer with more than 30 years of professional experience.
PLASTAR blown film line is committed to providing a personalized experience to users based on the performance standards of the blown film line you want to buy down to your lifestyle habits.
PLASTAR blown film lines have been designed to suit your needs completely; therefore, you can always request any type of blown film line that is specific to the purpose you want to serve.
This is why the features, performance rate, and functions of each PLASTAR blown film line differ because every blown film line is built with your specifications in mind.
PLASTAR blown film lines come in different types to suit your purpose and fit into a wide range of different applications you want to use your blown film line for, ranging from shrink wrap films, stretch films, barrier films, food packaging, shopping bags, and many more.
-
A20.
The prices of Blown Film Extrusion Machines vary depending on their functions and sizes.
You can get prices from the ranges of twenty thousand US Dollars to two hundred thousand US dollars.
You need to bear in mind that these machines cannot be sold at the same price in your different localities.
-
A21.
Due to the fact that the blown film extrusion line has passed the CE and SGS Certification of EU, making sure that all their products are safe and are fit for every environment all over the world without having to cause any issue for anyone, you cannot just get their product except you to make a reasonable payment.
Blown film extrusion line usually commences their production after they have received a payment that is about thirty percent of whatever product you are ordering.
Immediately that a certain amount has been deposited, work will begin in their company, and once they have almost finished carrying out the production, you will have to pay the remaining seventy percent of the product or products you ordered for.
Once you make the final payment, you will be sent pictures and video clips of the blown film extrusion lines when it is almost time for delivery. And after these criteria have been met, your blown film extrusion line will be packaged and shipped down to any location you're at.
-
A22.
After you must have paid completely for the blown film extrusion line and it has been shipped to your destination, engineers that must have been assigned from the blown film extrusion line company close to you would have been sent to your company before the actual time of debugging.
Upon the arrival of these engineers, they will assemble and debug the blown film extrusion lines depending on the setting of the factory.
Once they have confirmed that the machines are in good condition and can now work perfectly, they will begin training the members of staff of your company on how to operate the blown film extrusion lines, how to carry out production on it and how to perform routine maintenance of the blown film extrusion lines.
Blown film extrusion line manufacturers care so much about you and your company, and that is why engineers are sent across to you who will help in training your staff to ensure they are competent enough to carry out an operation on the blown film extrusion line effortlessly.
-
A23.
Multilayer blown film extrusion lines are produced to be suitable for a variety of applications, which include masking and shrinkable films, lamination, vacuum packaging, adhesive, agriculture, and many more.
Different types of raw materials can be used for multilayer blown film extrusion line extruder, and laminating each film layer to be suitable for the required properties isn't a necessity.
Multilayer blown film extrusion lines are suitable for the production of high-quality films.
However, two selections of dying rotating unit or Nip roll oscillating unit and three selections of winding system, Turret Touch and Gap Winder, Shaft Roll Winder, surface touch winder are recommended depending on the application and system of extrusion in multilayer blown film extrusion lines.
Multilayer blown film extrusion lines use a blend of two features of the PP material and the brightness features of PE material and can be classified into several types such as two-layer blown film extrusion line, three-layer blown film extrusion line, five layers blown film extrusion line, seven-layer blown film extrusion line and many others.
It helps to produce tubing in a single circumstance and regulates film width and thickness, which is -dependent on the capacity of air in the bubble, extruder output, and speed of the haul-off. It eradicates edge bead trim, and non-uniform temperature and enables biaxial orientation.
-
A24.
Purchasing used blown film extrusion machines is not advisable as they would be below standard in terms of quality, performance, and durability.
Investing in a new, quality blown film extrusion machine is a better choice as you would be guaranteed long-term efficiency and durability.
-
A25.
The recycled material refers to the plastic particles reshaped from recycled plastic film after being treated and then melted by a pelletizer.
The first-grade recycled material refers to the leftover material that is not contaminated with impurities, such as the edge of the online slitting of the blown film machine, and the plastic punched in the production of vest bags.
The recycled plastic particles processed with these leftover materials have better transparency. The quality of the particles formed by the pelletizer can rival that of the new material, so it is called the first-grade recycled plastic particles or the super-grade recycled plastic particles.
The second-grade recycled material refers to the recycled film that has been used once. It is judged by observing the transparency, brightness and surface roughness of recycled plastic particles formed by the pelletizer.
The third-grade recycled material refers to materials that have been used twice or more. The elasticity, toughness and other properties of the recycled plastic particles formed by the pelletizer are not outstanding, so the material can only be used for injection molding. The first-grade and second-grade recycled plastic particles can be used for film blowing.
Price grades of recycled materials:
- First-grade recycled plastic particles: 70-80% of the price of new raw materials;
- Second-grade recycled plastic particles: 50-70% of the price of new raw materials;
- Third-grade recycled plastic particles: 30-50% of the price of new raw materials;
- The above price ratio is for reference only
-
A26.
About 30% of food worldwide is wasted due to the lack of proper packaging. By 2050, the global population is expected to reach 10 billion. As urbanization is accelerated, proper food packaging is urgently needed during transportation from the place of origin to various cities to avoid unnecessary loss.
In addition, as the industry is growing, a great deal of food packaging applies barrier films from Blown Film Extrusion Lines to extend the shelf life, which reduces costs and increases sales and storage cycles.
Therefore, cutting-edge barrier films composed of 7 to 9 layers are in great demand in the food industry.
-
A27.
Compared with the single-layer blown film machine, the multi-layer co-extrusion blown film machine requires more screws and purchase costs to produce the film.
The selection of the multi-layer co-extrusion blown film machine depends on the application scenarios of the target film produced. If the film produced is mainly used as the packaging material for heavy packaging, high-end food bags, vacuum packaging bags, liquid packaging bags, etc., it needs functions including fragrance preservation, freshness preservation, corrosion protection, air tightness, and extended shelf life. A single-layer and single-characteristic film can never live up to these functions.
To produce a film that is qualified as a packaging material, and blow and co-extrude materials with a variety of characteristics(such as breathability, heat preservation, toughness, etc.) to form a multifunctional plastic composite film, we have to choose a multi-layer co-extrusion blown film machine.
The purpose we choose a multi-layer co-extrusion blown film machine is to give full play to the advantages of multiple materials and avoid the shortcomings of a single material or single-layer blown film machine. Taking the PP/PE co-extrusion blown film machine as an example, the machine combines the high hardness of the PP material and the high brightness of the PE material to produce a film that has the characteristics of both.
We have the following models of multi-layer co-extrusion blown film machines:
- Two-layer co-extrusion blown film machine,
- Three-layer co-extrusion blown film machine,
- Five-layer co-extrusion blown film machine,
- Seven-layer co-extrusion blown film machine, etc.
For example, The five-layer co-extrusion blown film machine mainly uses plastic particles with gas barrier properties, such as HDPE, MHDPE, LDPE, LLDPE, MLLDPE, PA, EVOH, etc., to produce food packaging films that require fragrance preservation, freshness preservation, corrosion protection, air tightness, and extended shelf life.
Multi-layer co-extrusion is to extrude multiple layers of plastic particles from one die at the same time. Most food packaging films and special films are produced by this co-extrusion lamination.
-
A28.
ABA three-layer blown film extrusion line and ABC three-layer blown film extrusion line are recommended for the production of agricultural seed packaging films.
The ABA three-layer blown film extrusion lines are effective for flexible production applications such as agricultural seed packaging films as they boost production and lower the cost of production.
The ABA three-layer blown film extrusion lines have two main motors that provide three-layer extrusion, the main machine gives the inner and the outer coating layers while the other machine is in charge of the inner filling layer; the goal of this to help you reduce cost and consumption while producing agricultural seed packaging films.
ABC three-layer blown film extrusion lines are designed to be used for the production of a wide range of packaging films such as agricultural seed packaging film, liquid packaging film, electrostatic protection film, and many others.
Both ABA three-layer blown film extrusion lines and ABC three-layer blown film lines have a high degree of hardness and resistance to wear, which makes them suitable for the production of agricultural seed packaging films.
-
A29.
The recommended blown film extrusion line used for the vacuum nylon packaging film is a five-layer blown film extrusion line.
PLASTAR's five-layer blown film line has been particularly designed to produce a wide range of applications such as oil packaging, milk bags, vacuum packaging of solid containers, and many more.
Five-layer blown film extrusion line, just like every other type of PLASTAR's blown film extrusion line, is equipped with dual-alloy forced-feeding screws that feature excellent hardness and wear resistance.
This makes the PLASTER five-layer blown film efficient in the production of vacuum packaging of solid containers as they have a high level of hardness and wear resistance.
Five-layer blown film extrusion lines also use an advanced five-layer plane stacking mold, which makes optimizes the layout due to thermofluidics, which helps watch the fluid condition through the 3D simulation software.
Five-layer blown film extrusion lines also help reduces the amount of time your blown film extrusion line is unavailable due to maintenance because it ensures the reduction of waste during the particle replacement procedure while printing vacuum Nylon packaging film.
-
A30.
ABA Three-layer blown film extrusion lines and ABC three-layer blown film extrusion lines, and ABA three-layer blown film extrusion lines are recommended for the production of permeable films.
ABA Three-layer blown film extrusion lines and ABC three-layer blown film extrusion lines help reduce production cost while producing materials and also has high wear resistance, thereby making them durable enough for the production of permeable films.
Both ABA three-layer blown film extrusion lines and ABC three-layer blown film extrusion lines are equipped with upgraded features such as centralized feeding, batching, and weight control, which are all blended into the touch screen to help enhance an easier and faster production of permeable films.
-
A31.
The blown film extrusion line that is used for PE/PA co-extrusion film is the five-layer co-extrusion blown film line.
This blown film extrusion line can be used to produce a variety of film packaging across different industries.
This blown film extrusion line has an excellent hardness feature, and it is highly wear-resistant.
It can produce a lot of films consequently without fail at a very high speed and high pressure.
The forced-feeding screw of this blown film extrusion line has a service life that is 3 to 5 times higher than an ordinary screw.
It has an advanced plane stacking mold that produces a high degree of polishing and coating of your materials, and it has the capability of cleaning itself after producing your material, with reduced wastage of material.
This lessens the downtime it has when a particle in it is being replaced or when the blown film extrusion line is being maintained.
Whether you want to produce PE/PA co-extrusion film or another packaging film, the five-layer co-extrusion blown film line will do the work while you don't have to worry about whether you will get a quality product because you will.
-
A32.
Extrusion molding is used due to its volume of productivity, speed, low cost, flexibility, and post-extrusion altercation option.
With extrusion molding, you can produce a large volume of plastics effectively and efficiently.
It is also cheaper than other molding types in that you can reuse waste materials, making production less expensive, unlike with other molding types like blow molding.
Your blown film extrusion machine can also work for long hours, allowing for long productivity time for as long as 24 hours in a day, increasing the productivity of your machine and products.
Extrusion molding is also flexible in that it is flexible in the production of materials, and can produce products with cross-section and products with mixed plastic attribute.
With extrusion molding, you can also alter production because after products are extruded, they remain warm, giving room for you to mold and remold them into more desirable shapes.
Your machine can produce up to 60 feet length products at a go. You tend to be more productive with extrusion molding, and at a cheaper cost compared to other molding types.
- A33. Blown film extrusion lines are used to produce polymer films used by packaging industries, which include shrinking wrap films, stretch films, packing films, shopping bags, laminating films, and many other packaging materials.
-
A34.
If you do thorough research, you will discover that about thirty percent of food across the globe gets to become waste as a result of lack of proper packaging.
Scientists have concluded that the population of the world is likely to reach several ten billion and when this is obtained, and even before then, provision should have been made for proper packaging of foods during the period of transporting them from one part of the world to the other to avoid loss.
Furthermore, as the industry grows, the packaging of food has been on the increase, and a great deal is applied to extend its longevity.
That is why blown film extrusion lines have been chosen over every other machine across the world to be used for the flexible packaging of food.
Blown film extrusion lines are generally accepted and chosen over other products by the global market because it is a technology-based enterprise that specializes in the operation and production of plastic packaging machinery.
Their main products are stretch film machines, multilayer co-extrusion internal cooling upper traction rotary blown film extrusion lines, and they are used in various industries such as electronics, logistics, chemical industries, construction, transportation, and food inclusive.
-
A35.
The PE shrink film can be produced with more than one blown film extrusion line, and you can try either of them.
The two blown film extrusion lines that you can use to produce PE shrink film are the ABA three-layer co-extrusion blown film line and the ABC three-layer co-extrusion blown film line.
The ABA three-layer co-extrusion blown film line is very flexible and can save your organization some production costs and conserve energy.
You can recycle materials for repeated production with this blown film extrusion line and save costs.
It also has a wear resistance, which gives you a competitive advantage, and at the same time, it helps you reduce cost, consumption, and energy and save the number of main machines.
The ABC three-layer co-extrusion blown film line is a general-purpose blown film line, and it can be used to produce different packaging films, including PE shrink film and other heavy packaging film.
Either of the blown film extrusion lines works for the purpose you want to use it for, and it will produce the PE shrink film you have in mind effortlessly.
Whichever one you go for, you can rest assured that you will get your desired result without defects.
-
A36.
The materials used for express envelop bags are the materials you can use with the ABA three-layer blown film extrusion lines and the ABC three-layer blown film extrusion line.
The material used in these blown film extrusion lines is HDPE, LDPE virgin raw material, recycled material, CaCO3 compound, biodegradable material, master starch, additive, mLLDPE, PP, EVA, LLDPE, etc.
If you want to produce quality express envelop bags, you have a range of material options to choose from.
-
A37.
The extrusion process is not suitable for iron and iron metal extrusion.
Producing an object with iron alloys may ruin your blown film extrusion machine because they are not fit for production.
Some of the plastic materials fit for the extrusion process are polyethylene, polypropylene, nylon, polycarbonate, acrylic, polyvinyl chloride, ABS, polystyrene, and nylon.
Any other material apart from the iron will extrude perfectly shaped objects that you have in mind.
The materials that are commonly used for extrusion are metals, polymers, ceramics, concrete, and foodstuff.
However, before you pick out the materials to use in your machine, consider the viscosity and the melting point differences of the materials.
The viscosity of material has to do with its resistance to flow. You know your material needs to flow so that it can be easily extruded out of the die.
-
A38.
The recommended blown film extrusion line for Milk bags is specifically of two types: AB two-layer blown film extrusion line and ABA three-layer blown film extrusion line.
The production line AB two-layer blown film extrusion line is suitable for blowing high-density polyethylene, low-density polyethylene, and linear low-density polyethylene, which are generally used in the production of courier bag film and two-color film.
ABA three-layer blown film extrusion line gives room for more flexible production than producing milk bags requires.
ABA three-layer blown film extrusion line also helps save energy consumption and cost, which makes producing milk bags cheaper for you.
The production line of both AB two-layer blown film extrusion lines and ABA three-layer blown film extrusion lines are equipped with advanced automation features such as centralized feeding, weight control, and batching.
All of these unique functions have been integrated into their touch screen to enhance productivity and ease during the production of milk bags.
-
A39.
The blown film extrusion extrusion line suitable for producing fruit bags is PLASTAR's single-layer blown film extrusion line.
The single-layer blown film extrusion line produced by PLASTER is most suitable for the production of fruit bags.
The single-layer blown film extrusion line helps you maximize the utilization of heat energy while producing fruit bags by putting an end to the use of cooling fans, thereby increasing your production output while reducing your energy consumption rate.
PLASTAR's single-layer blown film extrusion line makes use of a single-layer cone mold that helps reduce downtime maintenance and reduce particle waste in the particle replacement procedure in the production of fruit bags.
This happens because the single-layer cone mold ensures that each runner can clean itself under the PLASTAR's high-speed screws' intense pressure and high-speed scouring after the intense degree of polishing and coating.
-
A40.
Blown film extrusion can use plastic materials only.
The different types of plastic materials that can be used include:- PVC: PVC comes in different colors and levels of flexibility and rigidity and is highly durable.
- ABS: ABS is strong, and are commonly used to produce household materials.
- Thermoplastic elastomers: Thermoplastic elastomers are widely used due to their stability.
- Polyurethane: Polyurethane is commonly used in oil and gas industries due to its high abrasion resistance.
- Polypropylene: Polypropylene is strong and resistant to organic solvents.
-
A41.
Polyethylenes, which include LDPE, LLDPE, and HDPE polymers, are the most common materials used in blown film extrusion lines.
You need to understand the material properties of the resin you want to use for your blown film extrusion line.
As much as you would want to use as many materials as you want so as the maximize your blown film extrusion line utilization, it is also important to note that blown film extrusion lines are different and are not designed the same.
Therefore, blown film extrusion lines will not be able to accommodate all the types of materials available, which is why polypropylene and polyethylene (LDPE, HDPE, and LLDPE) are mostly used because they work effectively and with minimum complications with a majority of blown film extrusion lines.
-
A42.
The recommended blown film extrusion lines for high-barrier films are PLASTAR's 5-layer blown film extrusion lines.
PLASTAR's 5-layer blown film extrusion lines have been designed specifically to be used to produce symmetric barrier films and asymmetric barrier films.
PLASTAR's five-layer blown film extrusion line makes use of the most upgraded five-layer plane stacking mold, which helps optimize the layout due to the thermofluidics present and also monitors the fluid condition with the assistance of five-layer blown film extrusion line simulation software, which makes it efficient in the production of High Barrier films.
You do not have to worry about waste getting stored up in the waste and particle replacement place in the production of your high barrier films because the PLASTAR five-layer blown film extrusion line help reduce waste during production as each runner can clean itself under intense pressure and high-speed scouring of PLASTAR's high-speed screws.
Additionally, PLASTAR's 7/9 Layer Blown Film Extrusion Lines are also an excellent choice for producing high-barrier films. These lines offer lots of advanatges for this application.
-
A43.
The recommended blown film extrusion line for medical packaging firm is the five-layer co-extrusion blown film line.
The five-layer co-extrusion blown film extrusion line can be used to produce different products across different fields, and the medical field isn't left out.
It can be used to produce symmetric barrier film and asymmetric barrier film.
Therefore, if you want to produce any different medical packaging firm, your go-to blown film extrusion line is the five-layer co-extrusion blown film extrusion line.
You can make different packaging firms like medical mask packaging bags, outer packaging injection bags, medical mask packaging bags, disposable PE examination gloves, medical packaging bags, drip bags, and other packaging bags for different medical packages.
Although there are other blown film extrusion lines that can produce some of these medical packages, the five-layer co-extrusion blown film line can produce any medical packaging you want.
All you have to do is select the raw materials and produce any medical packaging accessories you want.
The five-layer co-extrusion blown film extrusion line is a good blown film extrusion line to use in producing all your medical packaging firms.
It is equipped with the necessary features needed to produce a variety of medical packaging firms.
-
A44.
The 5 layer Blown film extrusion machine is a type of blown film extrusion machine suitable for EVOH, Nylon, LDPE, and Metalloscenes and can be used for a wide range of applications such as lamination grade films, courier bags, oil packaging, and food packaging.
5 layer blown film extrusion machine helps increase your productivity and flexibility by helping you produce different varieties of products from a single line.
5 layer blown film extrusion machine guarantees that all property polymers have a thick skin layer and all cheap materials have a thick skin layer, thereby giving you room to produce different kinds of films to meet your specific needs.
5 layer blown film extrusion machine is equipped with the most advanced plane stacking mold, which helps you increase productivity and the quality of cooling.
The 5 layer blown film extrusion machine is your quick answer to achieve high-quality and detailed prints due to its advanced features.
-
A45.
Both the ABA three-layer blown film co-extrusion machine and the ABC three-layer co-extrusion machines are good, but they are quite different for the purposes you might intend for them.
ABA blown film machine is a general-purpose film production machine in that the production line of the ABC machine can be used to produce a wide range of products from packaging films, symmetrical film, liquid packaging film, electrostatic protection film, heavy packaging film, while ABC machine is a machine that gives you a competitive advantage over other types of blown film extrusion machine in that it is more flexible and saves more energy during production while you enjoy lower costs of machine and products.
Also, the ABA three-layer blown film co-extrusion machine has two main motors that provide three-layer extrusion, in which one of which is responsible for providing the inner and outer coating layers of your products, while the other main one produces the inner filling layer of your products.
It can also use recycled materials and calcium carbonate for up to 70% proportion of the materials used for production.
-
A46.
3-layer co-extrusion machine is a type of blown film extrusion machine used to produce greenhouse sheets, agricultural film, onstruction sheets, food packages, sacks, and many more.
3-layer co-extrusion machines are equipped with advanced automation functions for effective print production and are mainly of two types: ABA three-layer co-extrusion blown film extrusion machine and ABC three-layer co-extrusion machines.
ABA three-layer co-extrusion machine is equipped with two motors that produce the three-layer extrusion: the first machine produces the inner and outer coating layer while the other machine produces the inner filing layer, which helps conserve energy and reduce cost.
ABC three-layer co-extrusion machine can be used to produce liquid packaging film, electrostatic protection film heavy packaging film.
The Three-layer co-extrusion machine has an IBC cooling system inside the bubble, which increases its efficiency and provides low energy consumption.
Three-layer co-extrusion has the capacity to produce varieties of materials such as the LDPE, HDPE, PP, additives, masterbatches, sealant polymers, and lots more.
The short polymer flow passages of a three-layer blown film extrusion machine help speed up the extrusion process and enable you to change materials quickly.
-
A47.
Three-layer blown film extrusion lines are a type of blown film extrusion line used to make a plastic film or plastic sheet.
Three-layer blown film extrusion lines are produced with high-quality raw materials with upgraded technology in sync with the required standards.
Multilayer blown film extrusion lines are equipped with advanced automation functions like centralized feeding, weight control, IBC internal cooling, automatic central winding, and weight control. All of these functions have been merged on the three-layer blown film extrusion machine touch screen, thereby enhancing your productivity and making it easy for you to operate.
Three-layer blown film extrusion lines have many protection features such as puncture and heat resistance, reduced or no attraction to moisture and oxygen, and many others.
Three-layer blown film extrusion lines are an advanced feature and increased efficiency low energy consumption blown film extrusion line due to their IBC cooling system.
The most common raw materials used in three layers blown film line is HDPE, LDPE, LLPE, EVA, MPE, and PP.
Three-layer blown film extrusion lines can be used to produce a symmetrical film, shrink film, waterproof film in ponds, liquid packaging film, electrostatic protection film, and many others.
-
A48.
The 7, 9, and 11-layer blown film extrusion lines have several benefits over 3 and 5 layers blown film lines. First, with more layers, you can be creative with your production.
They offer a wide range of materials to choose from that will be in different layers.
With the 7-layer blown film line, you can cut the cost of production compared to 3 and 5-layer blown film extrusion lines.
It also has improved barrier or strength properties and toughness to produce different materials.
The 9 layers have a semi-rigid barrier structure, and its skin layers can be split into two to optimize performance and cost of production.
11 layers blown film line has an even higher barrier structure, and it can help you cut the cost of producing a particular application.
It has the flexibility to optimize barrier, rigidity, thermoformability, cost, and heat seal properties.
-
A49.
Stretch hood three-layer blown film extrusion lines are blown film lines used in producing a wide range of materials ranging from packaging materials, paper, etc.
This blown film extrusion line has many features like excellent melting homogeneity, smooth bore extruders, and triple lip air ring, which provides the blown film extrusion line with a cooling rate, easily exchangeable die, etc.
You can configure this blown film extrusion line in whichever way you want to produce the perfect product.
You can configure the material handling, extrusion, die, air ring, tower equipment, winding, control system, and optional services.
The three layers are low stretch, medium stretch, and high stretch.
The low stretch is below 35%, while the medium stretch is between 35% to 75%, and the high stretch is 75% and above.
-
A50.
3-layer co-extrusion plastic blown film lines are a type of blown film extrusion line used in the production of plastic filaments in making a wide range of product varieties.
It has different parts that work together in producing quality outputs.
It has an extruder that provides high melt quality under different temperatures while still maintaining an excellent output.
The dies of a 3-layer co-extrusion plastic blown film line are designed to produce a uniform thickness of the product and high production quality.
It usually has a high-performance motor with an AC inverter drive that allows you to produce your products easily while saving energy and minimizing maintenance.
It has a high lubrication system that helps to minimize the downtime of the blown film line.
The die heads of a 3-layer co-extrusion blown film machine are usually in three layers, and they all have inner cooling devices, while the air rings are double-lip air rings.
They have many features depending on their types and makers because there is a variety of 3-layer co-extrusion plastic blown film lines under different makers.
-
A51.
The Monolayer Blown Film Extrusion machine, also known as a single-layer blown film extrusion machine, is a type of Blown film extrusion machine specifically designed to print continuous lengths of plastic pieces from a specific resin type and is commonly used to produce agricultural covering film, degradable film, clothing bag film, and many others.
If you want to blow high and low-pressure polyethylene, then you should consider the Monolayer Blown Film extrusion machine as it puts an end to the usage of cooling fans and helps you make the best use of heat energy, thereby increasing production output and conserving energy rate.
A monolayer blown film extrusion machine makes use of a single-layer cone mold and also equips each runner with the ability to clean itself during intense pressure, thereby reducing the presence of dirt in the particle replacement area.
The monolayer blown film extrusion machine is equipped with advanced automatic functions such as weight control, automatic central winding, batching, and a lot more, which have been merged with the touch screen to aid your printing process.